AC5
F513, F115 (decarburization)
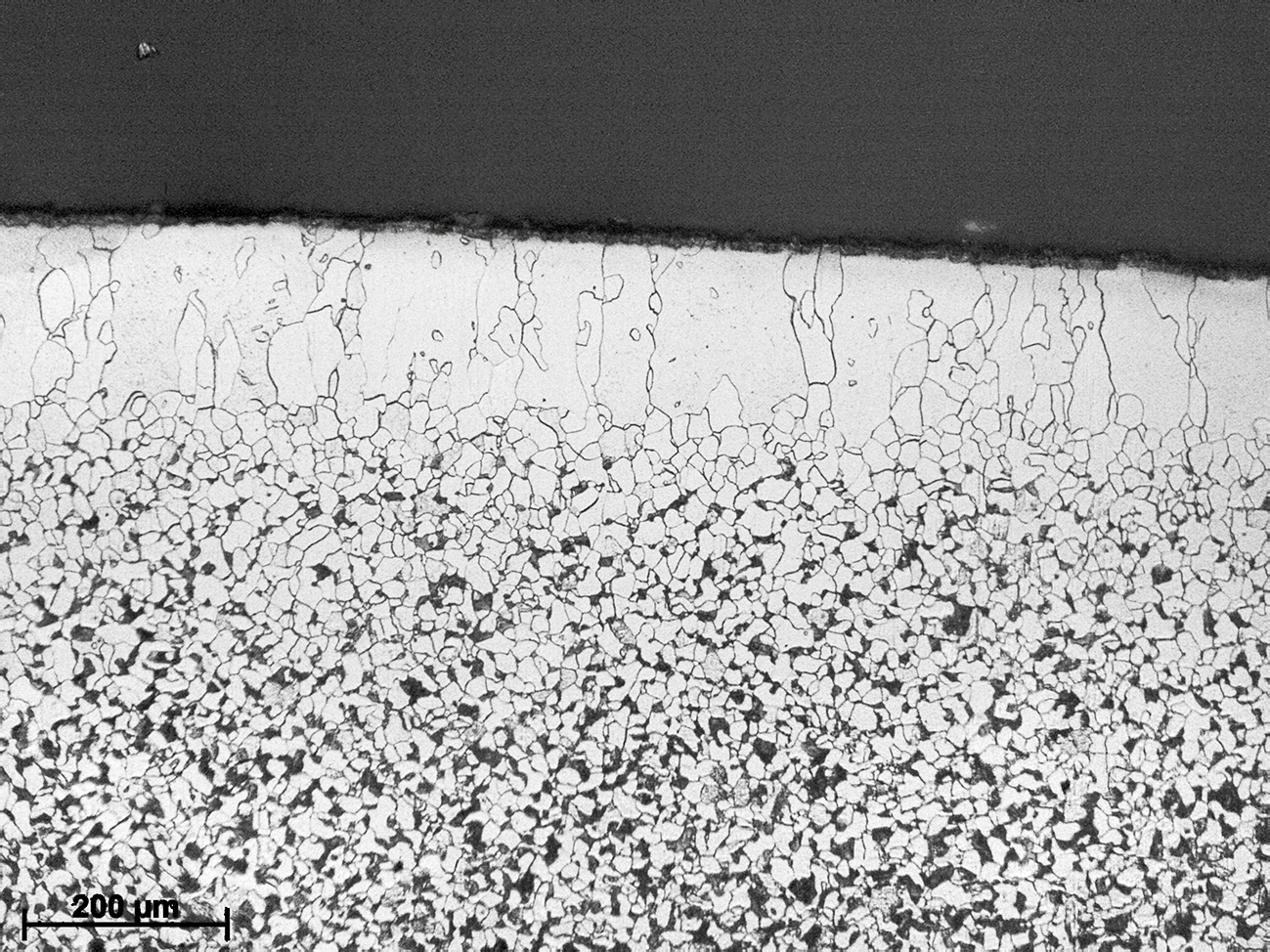
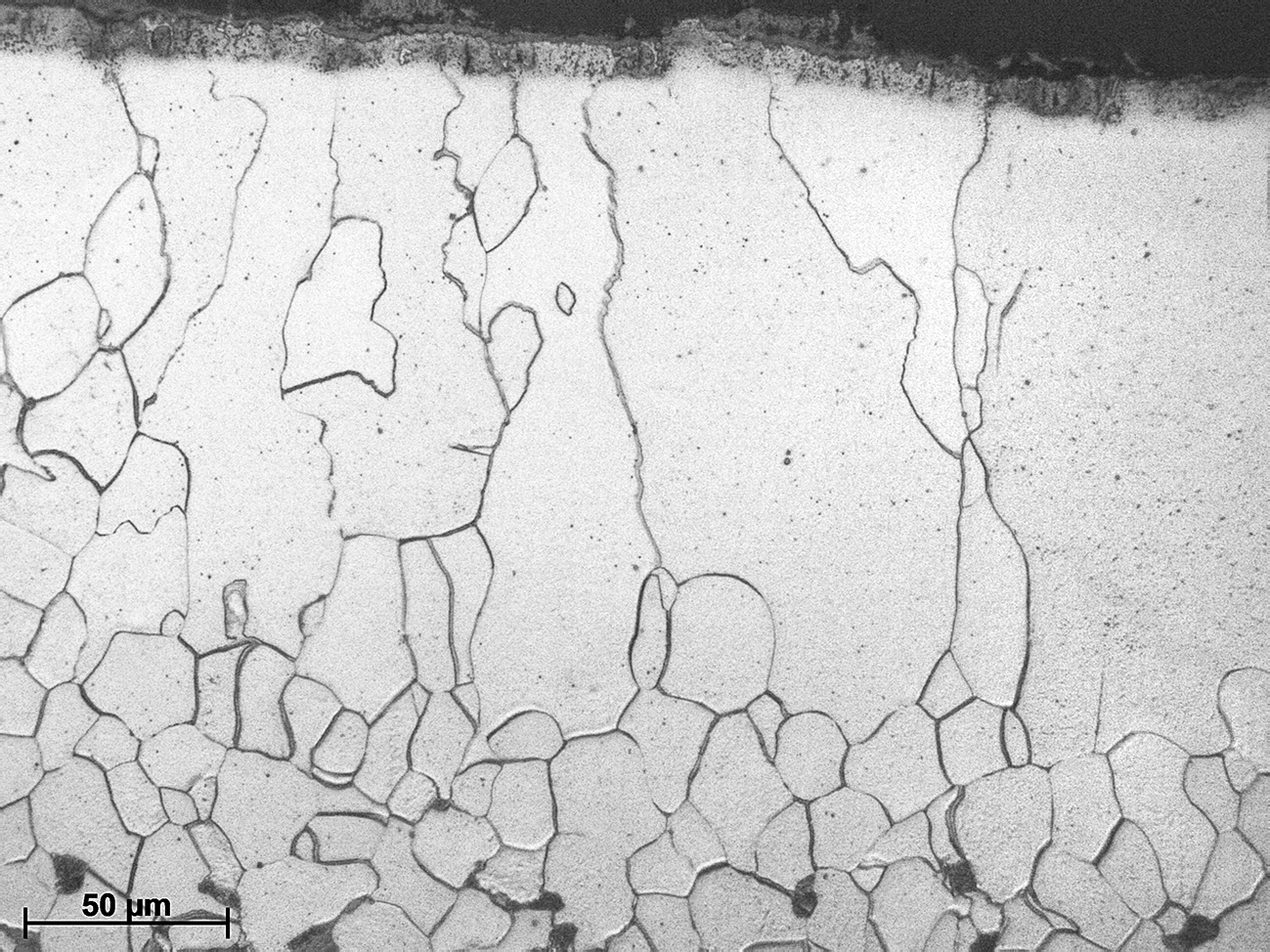
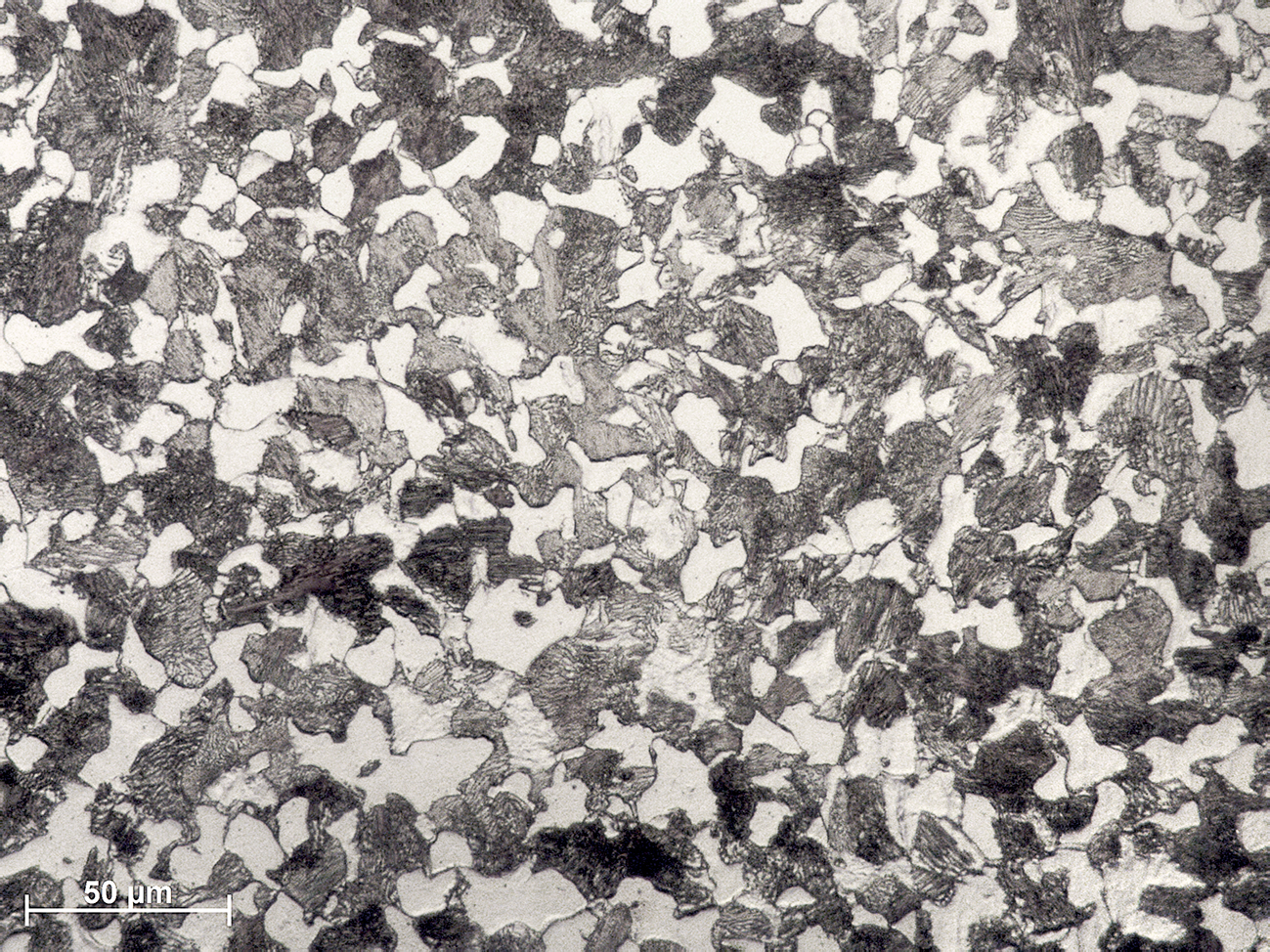
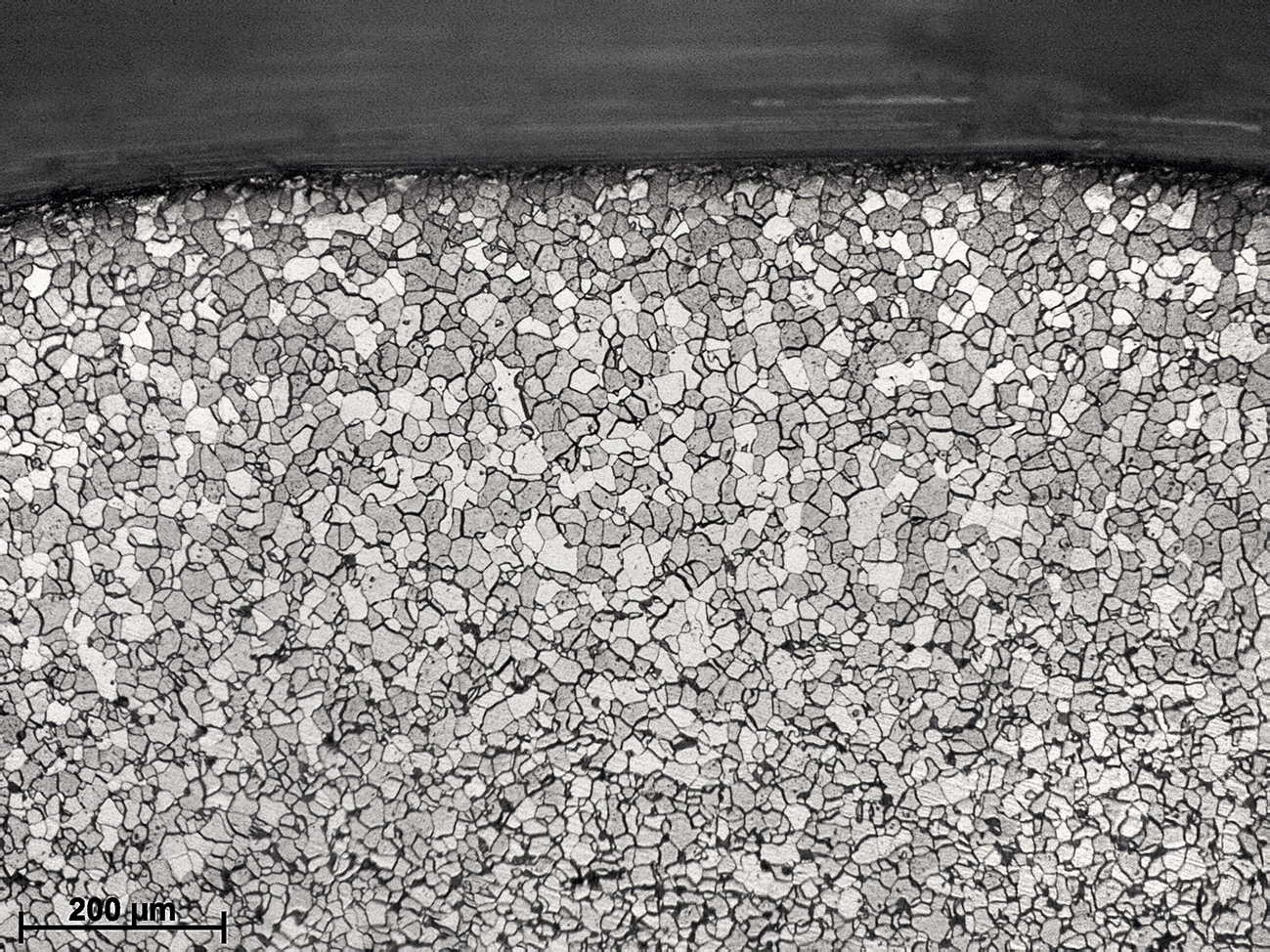
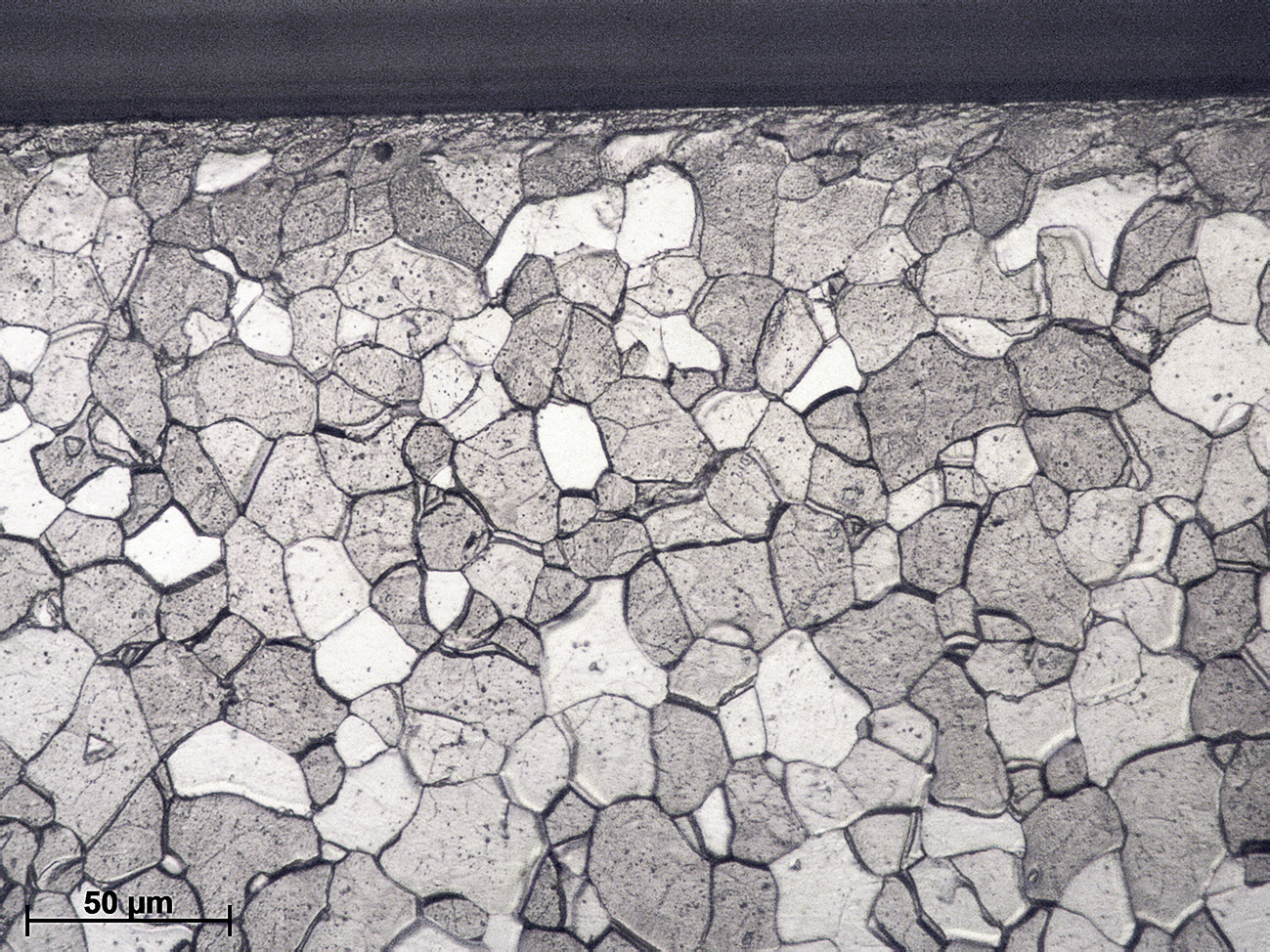
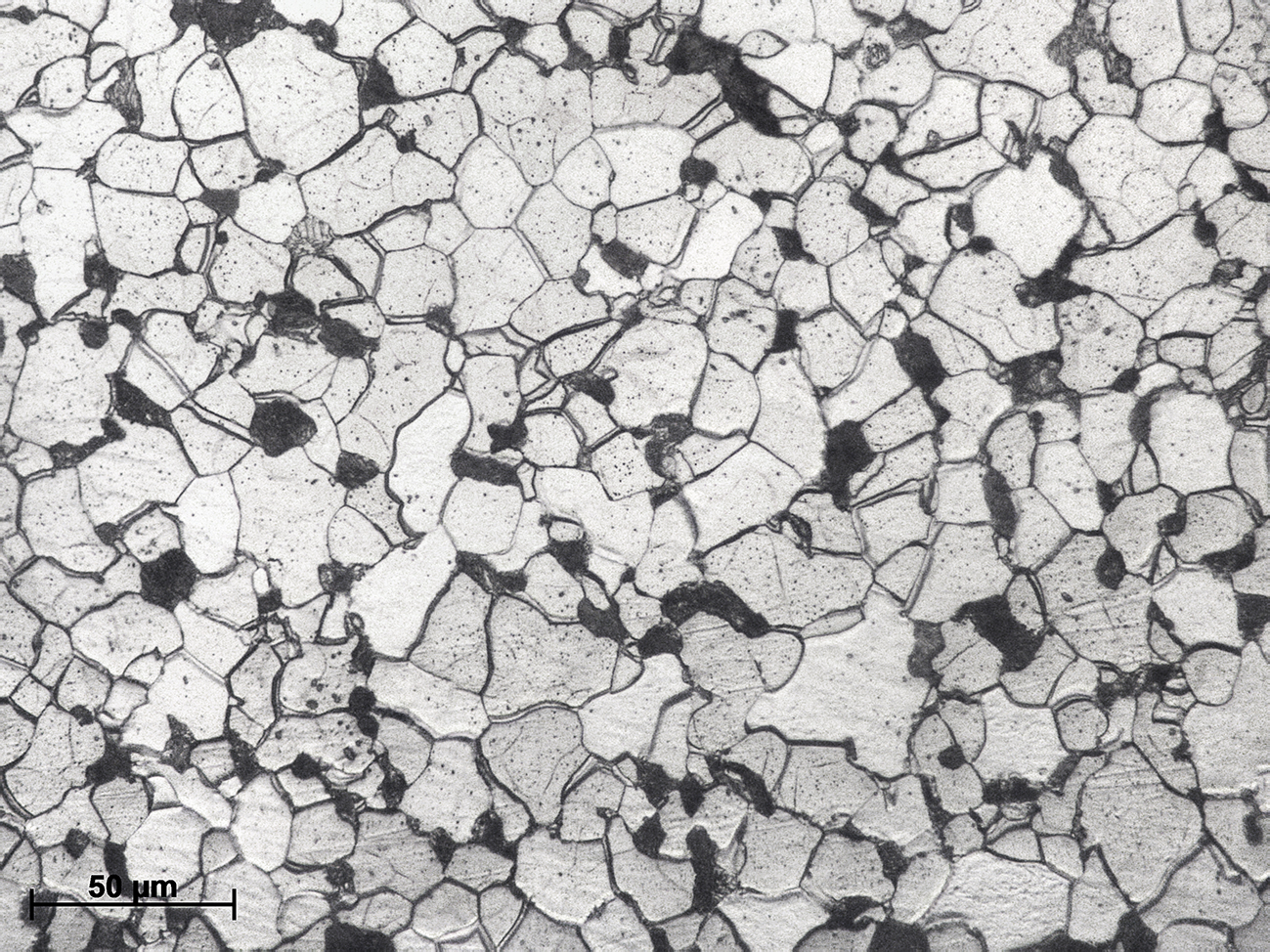
Composition:
F513 0.7-0.8 C; 0.25-0.50 Mn; <0.03 P; <0.03 S; 0.10-0.25 Si.
F115 0.52-0.60 C; 0.50-0.60 Mn; <0.03 P; <0.03 S; <0.30 Si.
Processing: Annealing (960ºC - 24 h) and Furnace cooling.
Etching: 15-30s immersion in 2% nital.
These micrographs show decarburization, a common defect in steels that have been subjected to heat treatment in an oxidizing atmosphere. Decarburization is particularly harmful in tool steels with high carbon content since the decarburized layer does not reach high hardness after quenching, thus reducing the tool performance in terms of wear resistance. Decarburization occurs due to reaction with atmospheric oxygen or other chemical species and is a common problem in forging and rolling operations as well as in heat treatments. This problem can be avoided by controlling the furnace atmosphere or by eliminating the decarburized layer by subsequent machining. There are, however, instances were the decarburized layer can be used as an advantage. The depth of the decarburized layer can be measured by following the ASTM E1077 standard.
It is interesting to note that depending on the temperature, cooling rate and type of steel it is possible to develop a decarburized layer with elongated and coarse ferritic grains. This is the case of the F513 steel in these micrographs. Also note the difference in the amount of pearlite between the bulk material and the surface.
This work is licensed under a Creative Commons Attribution-NonCommercial-ShareAlike 4.0 International License.