AC10
Corrugated steel bar (cross-section)
Composition: Corrugated steel (cross-section). 0.22%C-0.7%Mn-0.1%Si- 0.05%S-0.05%P. %Ceq= 0.34. The composition is within the ranges establisehd by the UNE 36 068 standard (0.24 %C max., 0.52 %Ceq, 0.055 %P max., 0.055 %S max. and 0.013 %N max. %Ceq = %C + (%Mn/6) + {(%Cr + %Mo + %V)/5) + ((%Ni + %Cu)/15}
Processing: hot-rolling of steel billets through rollers of decreasing diameter followed by finishing section to produce the ribs or the "tied knot" look. These
patterns increase the bond between steel and concrete. After the last rolling mill, the reinforcing bars (rebars) are water cooled following the Tempcore process (see diagram). In this process the bars are quenched from 1000 to 300ºC while the core remains hot. This results in tempering of the martensite formed at the surface. This sequence seeks to produce a steel bar that is tough (core) and with a high yield strength (surface).
Etching: 20-40 s immersion in 2%nital.
The macrostructure shows an outer dark region, two concentric circles and the core. In the core, the microstructure consists of ferrite and pearlite, whereas the outer region consists of tempered martensite. The transition zone may show bainite and other constituents.
Fe-Fe3C diagram
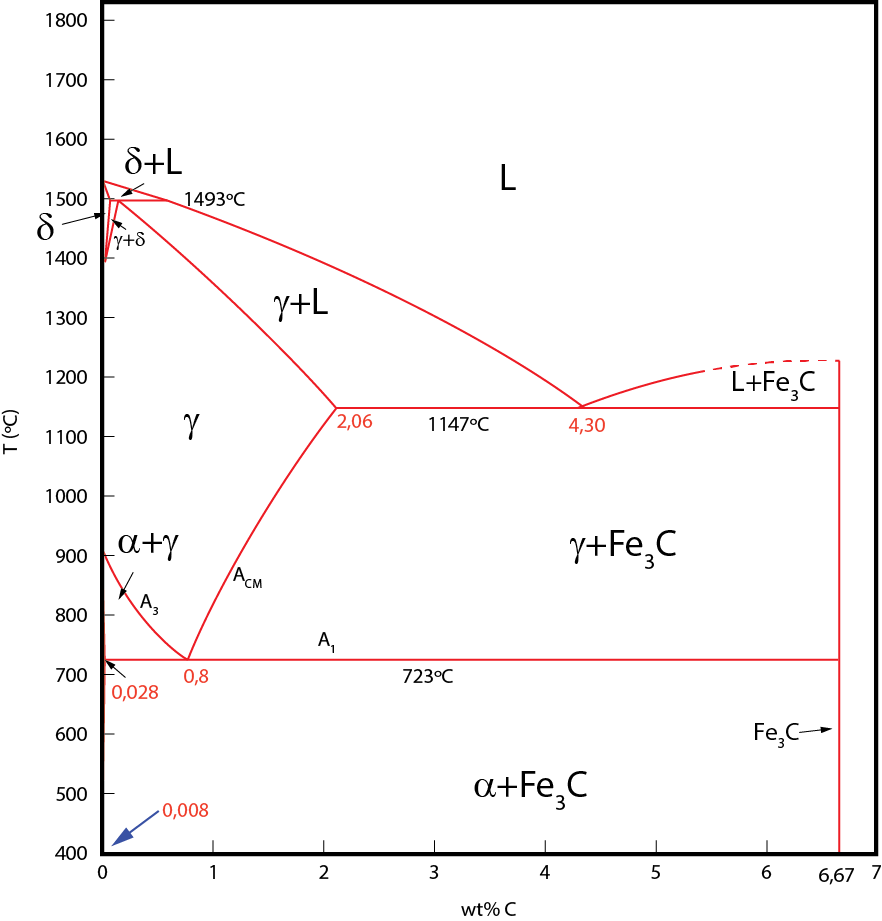
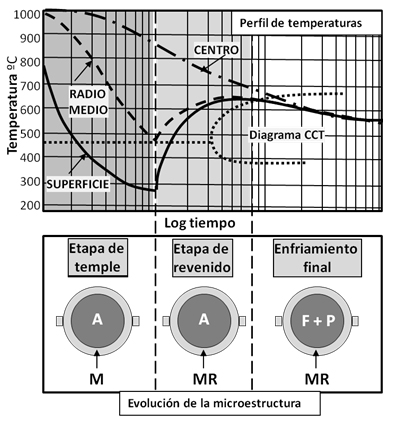
This work is licensed under a Creative Commons Attribution-NonCommercpial-ShareAlike 4.0 International