AC4
F513 (quench cracking)
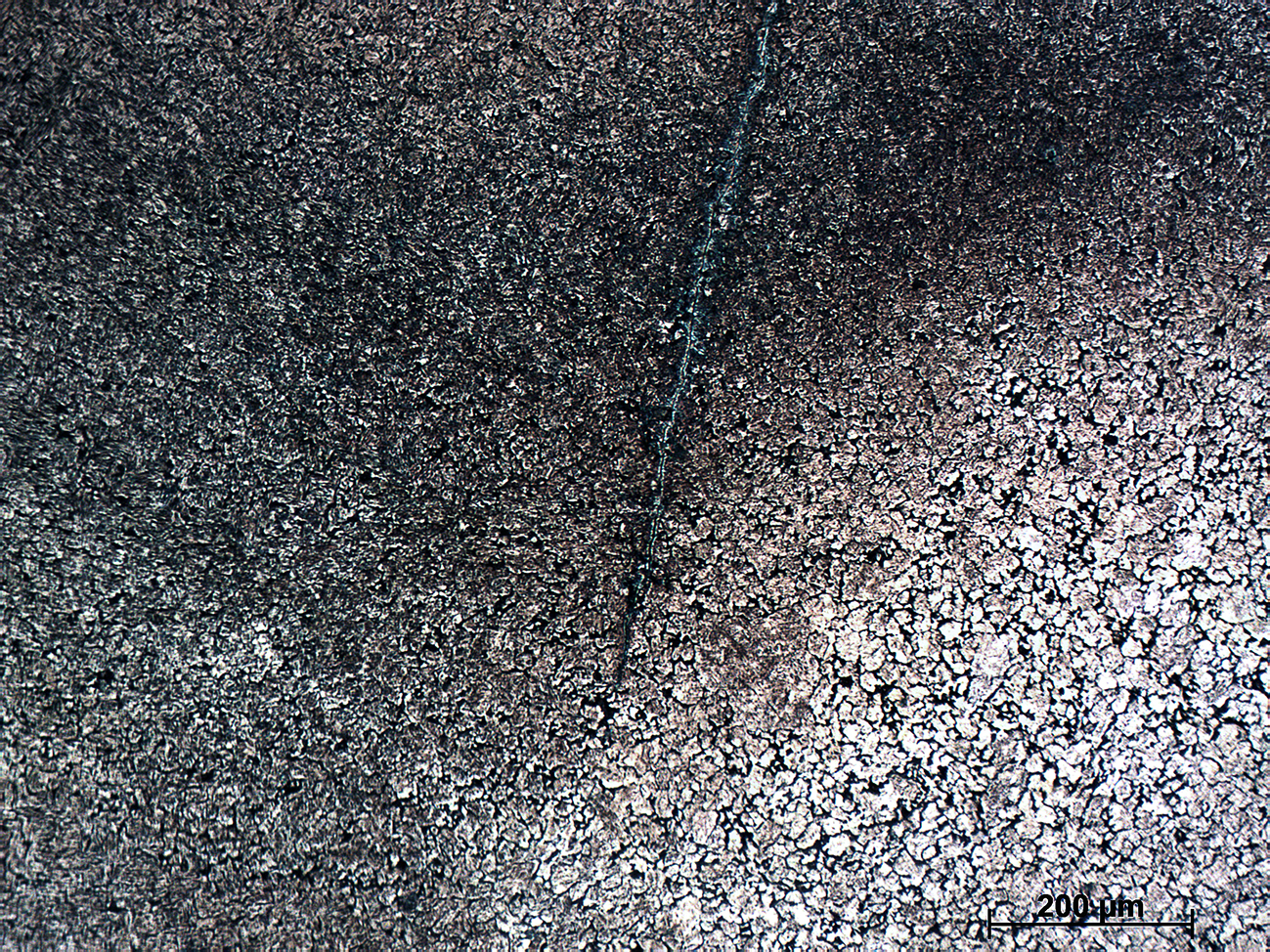
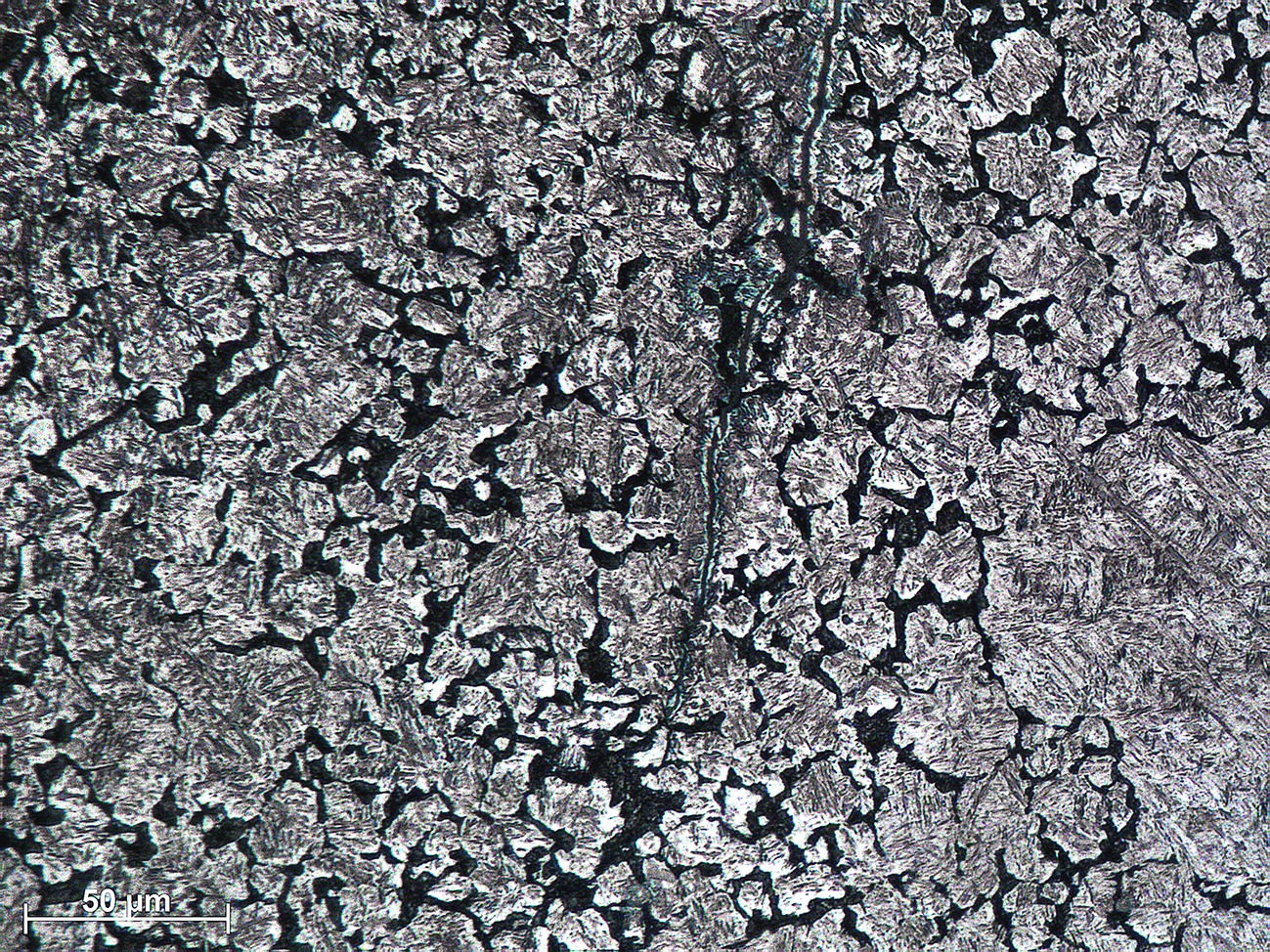
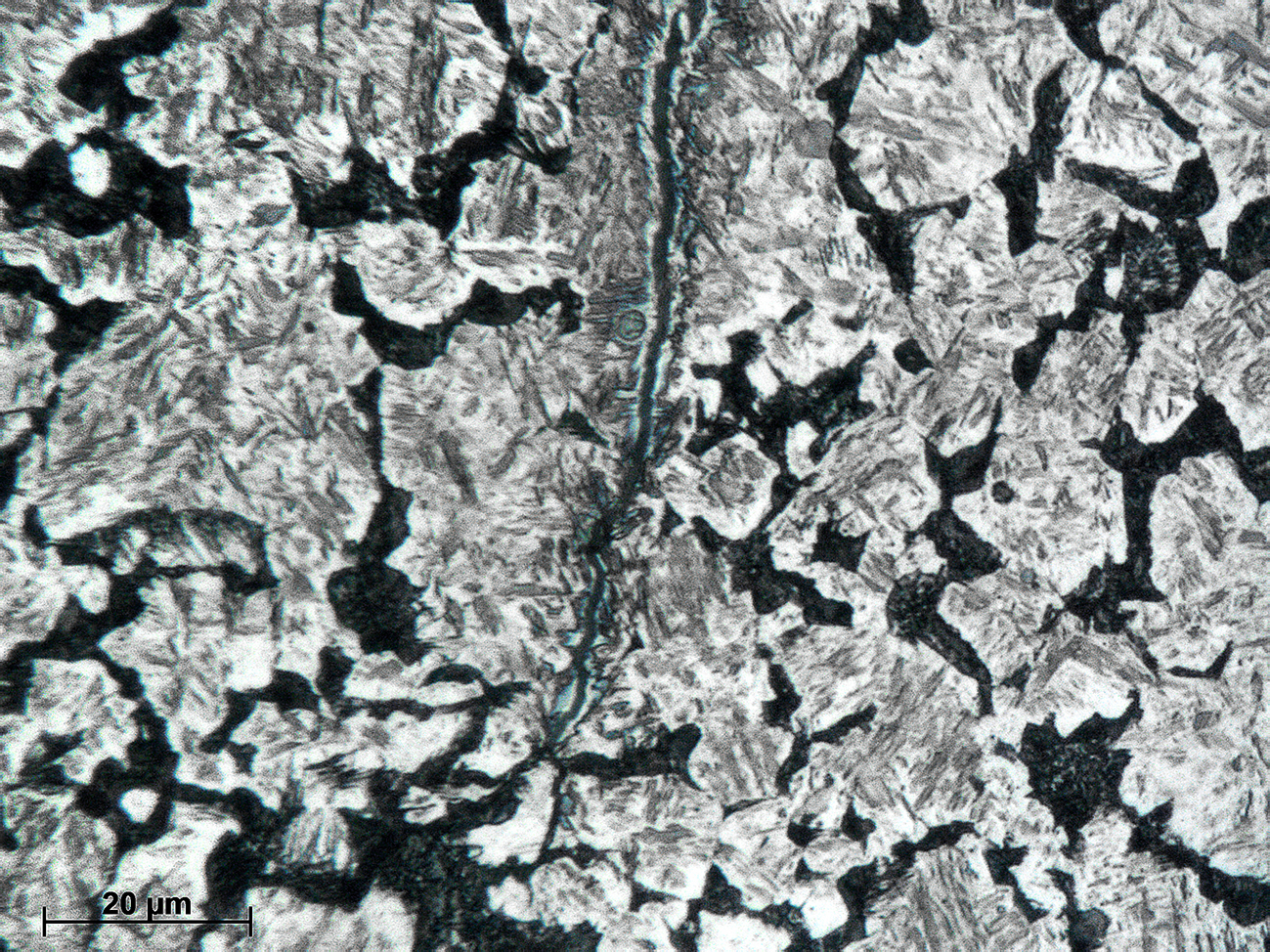
Composition: 0.70-0.80 C; 0.25-0.50 Mn; <0.25 Si; <0.03 P; <0.03 S.
Processing: Annealing (950ºC - 20 min), Water quenching and Impact
Etching: 15-30s immersion in 2% nital.
This is the same steel as AC3, but subjected to an impact after quenching. Due to the brittle nature of the quenched material cracks nucleate and propagate during impact. The micrographs show the presence of martensite laths/plates and fine pearlite at grain boundaries. Cracks show a jagged or crystalline path with almost no branching. These cracks are sometimes formed during quenching. Cracking occurs due to the thermal stresses originated from the differences in cooling rate between the surface and the bulk material. The surface cools down faster, resulting in the formation of martensite once the Ms temperature is reached. This results in volume expansion so the surface is under compression. Then, the interior of the material transforms to martensite but its expansion is restricted by the outer martensite layer, which is therefore placed in tension. If the ultimate tensile stress is exceeded the material will show intergranular cracking.
Machining after quenching is a common cause of cracking. Therefore, it is important to temper the material just after quenching in order to avoid cracking.
This work is licensed under a Creative Commons Attribution-NonCommercial-ShareAlike 4.0 International License.